TM 5-3825-226-24
AIR INLET AND EXHAUST SYSTEM
RESTRICTION OF AIR INLET AND EXHAUST
There will be a reduction of horsepower and
efficiency of the engine if there is a restriction in the air
inlet or exhaust system.
Air flow through the air cleaner must not have a
restriction of more than 25 in. (635 mm) of water
difference in pressure.
Back pressure from the exhaust (pressure
difference measurement between exhaust outlet elbow
and atmosphere) must not be more than 34 in. (864 mm)
of water.
MEASUREMENT OF EXHAUST TEMPERATURES
Use the 1P3060 Pyrometer Group to check
exhaust temperature. Special Instruction Form No.
SMHS7179 is the tool group and gives instructions for the
test procedure.
1P3060 PYROMETER GROUP
CYLINDER COMPRESSION
An engine that runs rough can have a leak at the
valves, or valves that need adjustment. Run the engine
at the speed that gives rough running. To find a cylinder
that has low compression or does not have good fuel
ignition, loosen a fuel line nut at a fuel injection pump.
This will stop the flow of fuel to that cylinder. Do this for
each cylinder until a loosened fuel line is found that
makes no difference in engine rough running. Be sure to
tighten each fuel line nut after the test before the next fuel
line nut is loosened. This test can also be an indication
that the fuel injection is wrong, so more checking of the
cylinder will be needed.
An analysis of the engine cylinder condition can
be done with controlled pressure air through the cylinder
head. Special Instruction GMG00694 explains the
procedure.
1.
Remove the fuel injection nozzle.
2.
Adapt an air hose to lP5564 Adapter. Install the
1P5564 Adapter in the fuel injection nozzle
opening in the cylinder head.
3.
Start crankshaft rotation until the piston in the
cylinder being inspected is at TC on the
compression stroke. In this position the valves of
this cylinder will be against their seats.
4.
Force the air into the cylinder and then check for
air leakage. An air leak from the exhaust opening
is an indication of exhaust valve leakage and an
air leak from the air cleaner inlet is an indication
of intake valve leakage. If the air leakage is into
the crankcase during this test, the piston or piston
rings can be the cause. VALVE CLEARANCE
SETTING Check and adjust valve clearance with
engine stopped. Valve clearance is measured
with a thickness gauge between the top of the
valve stem and the rocker arm.
VALVE CLEARANCE CHECK: ENGINE STOPPED
Exhaust ...................................................022 to .028 in. (0.56 to 0.71 mm)
Intake ......................................................012 to .018 in. (0.30 to 0.46 mm)
NOTE:
When
the
valve
lash
(clearance) is checked, adjustment is
NOT NECESSARY if the measurement
is in the range given in the chart for
VALVE CLEARANCE CHECK: ENGINE
STOPPED. If the measurement is
outside this range, adjustment is
necessary. See the chart for VALVE
CLEARANCE
SETTING:
ENGINE
STOPPED, and make the setting to the
nominal (desired) specifications in this
chart.
VALVE CLEARANCE SETTING: ENGINE STOPPED
Exhaust ...................................................025 in. (0.64 mm)
Intake ......................................................015 in. (0.38 mm)
To check and make adjustment to the valve lash, use the
procedure that follows:
1.
Remove the valve covers.
2-65
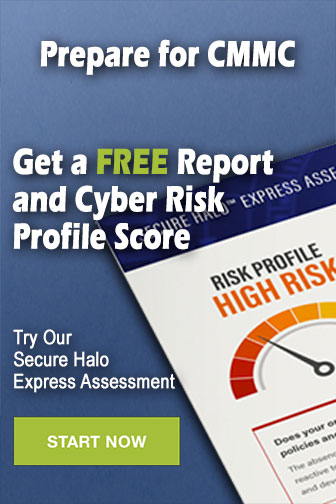