TM 5-3825-226-24
TESTING AND ADJUSTING
The 5S5123 Hydraulic Testing Group is used to
make the pressure test of the hydraulic system. Before
any tests are made, visually inspect the complete
hydraulic system for leakage of oil and for parts that
have damage. For some of the tests, a timer and a
measuring rule (either for inches or for millimeters) are
usable tools.
WARNING
When testing and adjusting the
hydraulic system, move the machine
to a smooth horizontal location.
Move away from machines that are at
work and any personnel. There must
be only one operator. Keep all other
personnel either away from the
machine or where the operator can
see the other personnel.
VISUAL CHECKS
A visual inspection of the hydraulic system and its
components is the first step when a diagnosis of a
problem is made. Stop the engine, lower the water
distributor to the ground and when the oil is cool so any
pressure in the tank will be at a minimum, make the
inspections that follow:
1.
Measure the oil level. Slowly turn the filler cap
until it is loose to let the tank pressure lower
before the filler cap is removed. Look for air in
the oil in the tank.
2.
Remove the filter element and look for particles
removed from the oil by the filter element. A
magnet will separate ferrous particles from
nonferrous particles (piston rings, O-ring seals,
etc.).
3.
Check all oil lines and connections for damage
or leaks.
OPERATION CHECKS
Checks of water distributor operation can be used to
find the source of oil leakage in the hydraulic system.
The oil in the hydraulic system must be at an operating
temperature of 1000 to 120OF (380 to 400C).
Drift of Lift Cylinders Check the drift of the lift
cylinders. Lift the bowl 6 to 10 in. (152 to 254 mm),
then move the control lever to the HOLD position. After
three minutes, put a mark on the side of the water
distributor at the bottom of the draft arm 6 in. (152 mm)
from the front of the distributor. After five minutes,
make the measurement for drift. Drift on a new
machine is not more than .31 in. (7.9 mm).
If the drift is too much:
1.
Check the carry check valves.
2.
Check the piston seals in the lift cylinders.
MEASURING DRIFT OF LIFT CYLINDERS
(Typical Example)
Travel Time of Lift Cylinders
Lower the water distributor to the ground. Run the
engine at high idle rpm. Use a stop watch to find the
time needed to fully lift the water distributor.
The time to lift the water distributor from the ground
to maximum height is approximately 2 seconds.
If the travel time is not correct:
1.
Check pump efficiency.
2.
Check the settings of the relief valve for the lift
cylinder circuit.
3.
Check the operation of the valve spool in the
control valve for the lift cylinders.
4.
Check the piston seals in the lift cylinders.
CHECKING PUMP EFFICIENCY
For any pump test at a given rpm, the pump flow
(gpm) at 100 psi (7.0 kg/cm2) (690 kPa) will be larger
than the pump flow (gpm) at 1000 psi (70.0 kg/cm2)
(6900 kPa).
The difference between the pump flow of two operating
pressures is the flow loss.
5-10
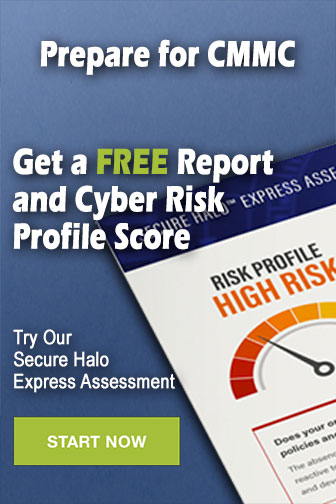