TM5-3820-256-1 u
(6) Water/Foam Injection Pump (6, Figure 1-2). This pump system injects water and foam into the drilling system
discharge line during certain drilling operations. It includes a high-pressure piston pump powered by a variable-speed
hydraulic motor. Foam concentrates are injected into the water discharge line by a pulse pump, at a controlled rate.
(7) Force Feed Lubrication System (7, Figure 1-2). This system provides lubrication into the air discharge line to
lubricate down-the-hole drilling tools. It includes a force feed pumping mechanism; it has two feeds and one check
valve.
(8) Break-out Tool Assembly (8, Figure 1-2). This device consists of a wrench and a hydraulic cylinder. It provides
a mechanical leverage to separate the drill pipe connections when the drill string is being removed from the hole.
(9) Rotary Drive and Rotary Table (9, Figure 1-2). The rotary table is driven by a hydraulic motor, through a 4-speed
transmission and a drive shaft. These components work together to provide the rotating motion that is then transferred to
the drill pipe, and therefore, to the drill bit.
(10)
Pulldown and Chain Feed (10, Figure 1-2). This system, most of which is mounted on the mast, includes a
hydraulic motor and a 2-speed transmission. Power from the motor/transmission is transferred to shaft sprockets, and
then to the chain which spans the length of the mast. The chains connect to a yoke that is attached to the rotary swivel.
When power is applied to the chains, pressure is transferred to the yoke, swivel, drill pipe, and subsequently, to the drill
bit.
(11)
Instruments (11, Figure 1-2). The controls needed to perform most of the drilling operations are located at the
left rear corner of the drilling rig. Gages and indicators provide sight readings of the various conditions of components of
the drilling rig. Some indicators and controls are located at other remote points around the drilling rig.
(12)
Hydraulic Jacks (12, Figure 1-2). Four hydraulic cylinders and jack baseplates are mounted to the drill frame at
each of the rig's four corners. Each cylinder is controlled, independent of the others, by hydraulic actuators on the
operator's control panel. The removable baseplates include security chains. Ample blocking is provided to ensure rig
stability in sandy locations.
(13)
Winch Assembly (13, Figure 1-2). A hydraulically driven, 20, 000 pound capacity winch is mounted on the front
bumper of the drilling rig truck. It is operated from inside the truck cab by an air-shift control. Normally, the winch is
used for non-drilling related operations, such as pulling the drilling rig, or other vehicles, from difficult-terrain situations.
1-6
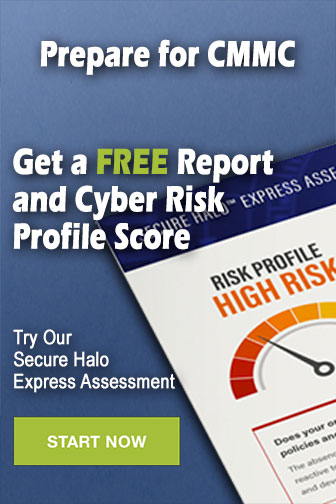