TM 5-3825-226-24
FUEL INJECTION LINES
Fuel from the fuel injection pump is sent through the
fuel injection lines to the fuel injection nozzles.
Each fuel injection line of an engine has a special
design and must be installed in a certain location.
When fuel injection lines are removed from an engine,
put identification marks or tags on the fuel lines as they
are removed, so they can be put in the correct location
when they are installed.
The nuts that hold a fuel injection line to an injection
nozzle and injection pump must be kept tight. Use a
torque wrench and the 5P144 Fuel Line Socket to
tighten the fuel line nuts to 30 ± 5 lb. ft. (40 ±7 N-m).
FUEL INJECTION PUMPS
When injection pumps, sleeves and lifters are
removed from the injection pump housing, keep the
parts of each pump together so they can be installed
back in their original location.
Be careful when disassembling injection pumps. Do
not damage the surface on the plunger. The plunger,
sleeve and barrel for each pump are made as a set. Do
not put the plunger of one pump in the barrel or sleeve
of another pump. If one part is worn, install a complete
new pump assembly. Be careful when putting the
plunger in the bore of the barrel or sleeve.
When an injection pump is installed correctly, the
plunger is through the sleeve and the adjustment lever
is engaged with the groove on the sleeve. The bushing
that holds the injection pump in the pump housing must
be kept tight. Tighten the bushing to 60 ± 5 lb. ft. (80 ±
7 Nm). Damage to the housing will result if the bushing
it too tight. If the bushing is not tight enough, the pump
will leak.
AIR INLET PIPE
(Typical Example)
CAUTION
If the sleeves on one or more of the fuel
injection pumps have been installed wrong,
damage to the engine is possible if cautions are
not taken at first starting. When the fuel
Injection pumps have been removed and
Installed with the fuel injection pump housing
on engine, take the following cautions when
first starting the engine.
a.
Remove the air cleaner leaving the air
inlet pipe open as shown.
b.
If the sleeve on a pump has been
installed wrong and the engine starts to
run too fast, put a steel plate over the air
inlet opening as shown to stop the engine.
STOPPING THE ENGINE
(Typical Example)
FINDING TOP CENTER COMPRESSION POSITION
FOR NO. 1 PISTON
No. 1 piston at top center (TDC) on the
compression stroke is the starting point for all timing
procedures.
1.
Remove the plug from the timing hole (2) in the
front cover. Put bolt (I) in timing hole (2).
The bolt from hole (3) can be used.
2.
Turn the crankshaft COUNTERCLOCKWISE
(as seen from rear of engine) until bolt (I) will go
into the hole in the drive gear for the camshaft.
3.
Remove the valve cover on the right side of the
engine (as seen from rear of engine). The two
valves at the right front of the engine are the
intake and exhaust valves for No. I cylinder.
2-48
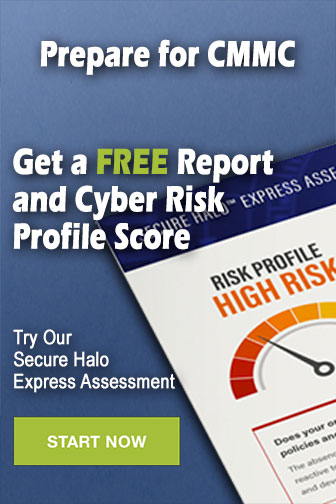