TM 5-3825-226-24
GOVERNOR PARTS
23. Piston for dashpot governor. 24. Spring for
dashpot governor. 26. Spring seat. 27. Over fueling
spring. 28. Thrust collar.
When governor springs (25) are put in compression, the
spring seat at the front of the governor springs will make
contact with load stop lever(29). Rotation of the load
stop lever moves load stop pin (17) up until the load
stop pin comes in contact with the stop bar or stop
screw. This stops the movement of thrust collar (28),
the connecting levers, and sleeve control shafts (19). At
this position, the maximum amount of fuel per stroke is
being injected by each injection pump.
The carrier for governor weights (30) is held on the rear
of camshaft (13) by bolts. When engine rpm goes up,
injection pump camshaft (13) turns faster. Any change
of camshaft rpm will change the rpm and position of
governor weights (30). Any change of governor weight
position will cause thrust collar (28) to move. As
governor weights (30) turn faster, thrust collar (28) is
pushed toward governor springs (25). When the force
of governor springs (25) is balanced by the centrifugal
force of the governor weights, sleeves (32) of the
injection pumps are held at a specific position to send a
specific amount of fuel to the engine cylinders.
When the governor control lever is turned toward the
FUEL-OFF position with the engine running, there is a
reduction of force on governor springs (25). The
movement of the linkage in the governor will cause fuel
control shafts (19) to move sleeves (32) down, and less
fuel will be injected in the engine cylinders.
To stop the engine, turn the ignition switch to the "OFF"
position. This will cause the shut-off solenoid to move
linkage in the fuel pump housing. Movement of the
linkage will cause sleeve levers (31) to move sleeves
(32) down, and no fuel is sent to the engine cylinders.
With no fuel going to the engine cylinders, the engine
will stop.
14. Housing for fuel injection pumps. 19. Sleeve
control shafts. 31. Sleeve levers. 32. Sleeves.
FLOW OF FUEL USING THE PRIMING PUMP
When the handle of priming pump (2) is pulled out,
negative air pressure in priming pump (2) opens check
valve (A) and pulls fuel from fuel tank (7). Pushing the
handle in closes check valve (A) and opens check valve
(B). This pushes air and/or fuel into housing (14)
through the fuel passages and check valve (C). More
operation of priming pump (2) will pull fuel from fuel
tank (7) until the fuel lines, fuel filter (9) and housing
(14) are full of fuel. Do this until the flow of fuel from
manual bleed valve (5) is free of air bubbles. Relief
valve (10) will open and let the fuel go to the inlet for
fuel priming pump (2) if the pressure gets higher than 20
psi (140 kPa) when using priming pump (2).
CONSTANT BLEED VALVE
CONSTANT BLEED VALVE
4. Constant bleed valve. D. Check valve.
2-9
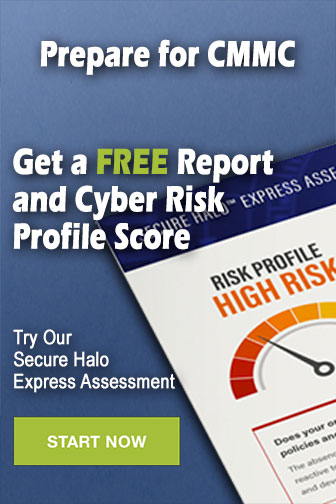