SERVICE MANUAL
During next check, 379-414 kPa (55-60 psi) air
pressure needs to be maintained at control port (H) and
tractor emergency port (G).
Connect air line with gauge and shut-off valve to
tractor service port (F). Open valve to build 345 kPa (50
psi) pressure and shut off valve. Trailer service gauge
must show build up pressure. While maintaining steady
pressure of 379-414 kPa (55-60 psi) at pressurized
ports, permissible leakage at exhaust port is 25 mm (1")
diameter bubble in three (3) seconds. Disconnect air
pressure to tractor service port (F). Trailer service port
pressure must exhaust to zero.
Begin with manifold pressure supplying both control
and tractor emergency ports (G and H) at 681-861 kPa
(100-125 psi). Shut off manual valve and disconnect air
source. Open manual valve slowly and allow manifold
pressure to bleed down to 272 kPa (40 psi) and close
manual valve. Air pressure at trailer emergency port (D)
should have exhausted to zero. While maintaining steady
pressure of 138-172 kPa (20-25 psi) at control port (H)
and tractor emergency port (G), connect air to tractor
service. Open manual valve to build up 345 kPa (50 psi)
pressure. Gauge at trailer service (E) must not show
pressure. Disconnect all air lines and gauges and
remove pipe plugs where used.
DISASSEMBLY
Refer to Fig. 2 for numbers in parenthesis.
After valve is disconnected and removed from
tractor, inspect it visually for damage. If casting is broken
or shows fractures, replace valve.
To disassemble valve, place hand force against end
cap (3) while carefully removing snap ring (1) by prying it
out of the groove. (Pulling exposed end of snap ring
straight out will distort it.) Spring (19) will push end cap
(3) and piston (17) out of body (20). Remove spring (19)
and O-ring (2) from body. End cap (3) and piston (17)
can be separated easily.
Maintain finger force against end cover (9) while
removing four screws (11) and four washers (10).
Carefully allow spring (12) to free height.
Remove end cover, spring and valve (13). Be alert
for spring (6) to push out spool (7). Remove spool, spring
and exhaust valve assembly (5) from body. Remove O-
rings (4), (8), (14), (15), (16), (18) and (21) from pistons,
spool and cover. (Remove metal retainer and rubber
seal from assembly (5).
CLEANING AND INSPECTION
Wash all parts in clean mineral spirits or equivalent
cleaning solvent and then dry.
Examine rubber valve seals and O-rings. Rubber
parts must be free of cuts, nicks or tears.
Examine end cap, pistons and spool. All contacting
surfaces for O-ring seals must be smooth and round and
free of deep scratches, dents or gouges. Valve seats at
end of piston tubes and spool must be flat and smooth
showing no dents or distortion. Spool must not be
fractured or have pieces broken out. Flange on piston for
valve assembly (5) must not be dented or bent.
Examine valve body and end cover. Castings should
be free of cracks and voids. All surfaces for O-ring seals
must be smooth and round and free of deep scratches,
dents or gouges. Small hole passage from control port
into main bore must not be plugged. Mating surfaces of
valve body and end cover flange must not be dented or
bent. Snap ring groove in valve body must not be
distorted and must be free of corrosion. Valve body seat
must be flat and smooth, free of dents and deep
scratches. Examine springs, valve retainer, snap ring,
screws and washers. Parts should be free of distortion
and corrosion.
Replace parts that show any of the above defects.
It is recommended that all rubber parts be replaced
with new parts supplied in the repair kit.
REASSEMBLY
Lubricate O-rings and valve seal and all O-ring
sealing surfaces and bearing surfaces on pistons, end
cap, cover, spool and body. Apply a thin film of Item 3 of
LUBRICANT SPECIFICATIONS.
Install O-ring (15), valve seal and retainer washer to
make exhaust valve assembly (5). Install assembly (5)
into valve body (20). Install spring (6) with large end
against exhaust valve retainer. Install O-rings (8) and
(16) on spool (7) and O-ring (14) on end cover (9). Place
spool on spring (6) with spool seat facing out. Place
spring (12) and rubber valve (13) on top of spool (refer to
Fig. 2 to see position of valve to spring). Align end cover
(9) to valve (13) and body (20). Push gently and firmly to
compress spring (6) until cover contacts spool. Continue
pressing spool into body. Hold end cap and install four
washers (10) and screws (11). Tighten screws to 6-7
Nm (50-60 in lbs) torque.
Install spring (19) into valve body (20). Install O-rings
(4), (18) and (21) on piston (17).
Install O-ring (2) on end cap (3) and mate piston to end
cap. Install piston and end cap on spring. Align and push
end cap firmly into body and hold to prevent spring from
CTS-4079 - CHAPTER XI - Page 5
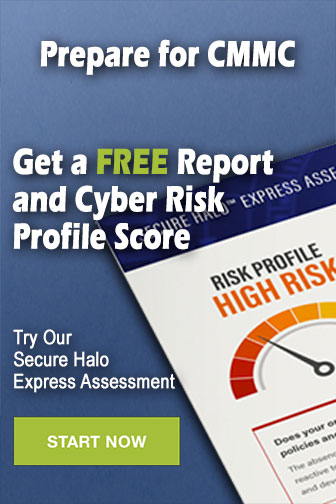