SERVICE MANUAL
b.
Air usage exceptionally high and not normal
for a highway vehicle. This may be due to
accessory air demands or some unusual air
requirement
that
does
not
allow
the
compressor
to
load
and
unload
(compressing and noncompressing cycle)
in a normal fashion. Check for high air
system leakage.
c.
The air dryer has been installed in a system
that has been previously used without an air
dryer. This type system will be saturated
with
moisture
and
several
weeks
of
operation may be required to dry it out.
d.
Location of the air dryer is too close to the
air
compressor.
Refer
to
"Installation"
section.
2.
Check mounting bolts for tightness. Check all
air and electrical connections.
3.
Check the operation of the integral single check
valve in the AD-2 or the "in-line" check valve
used with AD-1. Build the air system to governor
cut-out and observe the test air gauge installed
in the supply reservoir. A rapid loss of pressure
could indicate a failed check valve. This can be
confirmed by checking at the purge valve
exhaust.
Purge valve will be open when governor cut-out
pressure is reached. Allow two minutes for purge
cycle before testing the check valve.
4.
Check for excessive leakage at the purge valve
by coating the exhaust with a soap solution while
the compressor is loaded (compressing air).
5.
Check the operation of the safety valve by
pulling the exposed stem while the compressor
is loaded (compressing air). There must be an
exhaust of air while the stem is held and the
valve should reseat when the stem is released.
6.
Check all lines and fittings leading to and from
the air dryer for leakage and integrity.
7.
Check
the
operation
of
the
heater
and
thermostat during cold weather operation. This
can be done by allowing the end cover assembly
to cool below 100 C (500 F) and feeling the end
cover when the ignition is turned on. The end
cover should be warm to the touch within a few
moments. Warming should cease at about 30C
(85).
The desiccant change interval may vary; however, it
is generally recommended that the desiccant be
replaced every 12 months (yearly). If experience has
shown that extended or shortened life has resulted for a
particular installation, then the yearly interval can be
increased or reduced accordingly.
REMOVAL OF DESICCANT CARTRIDGE
AD-1 & AD-2
1.
Make certain the vehicle is safely parked. Block
the wheels if necessary.
2.
Drain the air system completely being sure that
the lines leading into and out of the air dryer are
at atmospheric pressure.
3.
Disconnect the air line from the end cover and
mark location of this port on the dryer.
4.
Disconnect the heater wire.
5.
Loosen the three capscrews on the end cover
and turn the retaining clamps aside (capscrews
may be left finger tight) .
6.
Locate the notch in the dryer shell. While
pushing the end cover up into the dryer, insert
the blade of a screwdriver in the notch and
slowly pry out the retaining ring. Remove the end
cover assembly and set it aside temporarily.
7.
Using a 3/4" socket wrench, remove the
cartridge and desiccant sealing plate assembly.
Be certain the desiccant sealing plate
assembly comes out with the cartridge.
REMOVING AND REBUILDING DESICCANT
SEALING PLATE
Before the desiccant cartridge can be replaced or
rebuilt the desiccant sealing plate must be removed. It is
recommended that all non-metallic parts be replaced
when the plate is removed. In the past, three methods
have been employed to secure the desiccant sealing
plate to the desiccant cartridge, a Tru Art retaining ring,
two special thin nuts and the latest method a single hex
lock nut. Removing the securing device will permit the
desiccant plate to be separated from the desiccant
cartridge. After removing the desiccant cartridge:
1.
Remove the two o-rings from the desiccant plate
and discard them.
CTS-4079 - CHAPTER XIV - Page 6
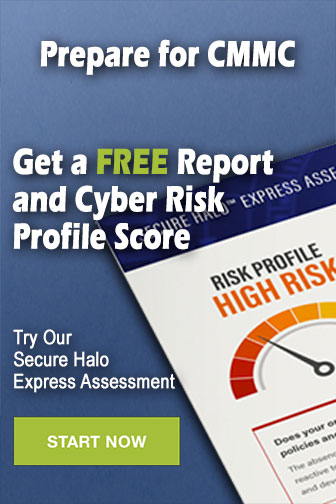